Creating an Effective Safety Eyewear Program
Employers commit time and energy to purchasing and providing personal protective equipment (PPE) to their employees. Yet, an estimated 2,000 work-related eye injuries occur every day in the United States with more than 75% of those injuries being a result of employees choosing to not wear the eye protection provided for the assigned task.
Beyond the injury, costs to the employee and employer are significant. The injury can adversely alter the employee’s quality of life, finances, family relationships, and daily routines, whether at home or on restrictions at work.
Employer costs include time and resources committed to the incident investigation and direct medical costs under workers’ compensation for treatment. Indirect costs include overtime or replacing the injured employee, follow-up physician appointments, training another person to perform the injured employee’s tasks, and employees and community perceptions about the employer’s leadership and brand reputation. If an injury is reportable (vision loss), the employer can also expect an OSHA investigation.
Using the OSHA Safety Pays calculator, a vision loss injury directly costs over $75,000. Indirect costs add another $83,000 to the loss. At a 3% profit margin, additional sales of more than $5MM is needed.
These costs are not budgeted but are taken from the company’s bottom line. Significant or multiple injuries cost everyone performance bonuses, profit-sharing, and overall business success.
So, why do employees choose to not wear the provided eyewear? Ask your employees and you will likely hear:
- It’s uncomfortable (too hot, poor fit, discomfort)
- I can’t see (fogging and/or visual distortion)
- I don’t need it (no perceived hazard)
- I look stupid (not fashionable)
Selecting safety eyewear cannot be based only on price. If employees will not wear the eyewear, the “price savings” doesn’t matter – especially if you experience a $150K injury, lose a valued and experienced employee, and your remaining employees perceive that your interests are more in saving money than in saving them.
So, what is necessary for your safety eyewear program to be effective? You have likely conducted the risk assessment and already know your employees’ hazard exposures. The task is to help employees understand the risks and find eye protection that does more than meet ANSI Z87+ requirements, but also meets your employees’ needs.
- If you cannot eliminate the hazards, choose:
- Safety glasses – flying debris, particulates
- Vented safety goggles – fines, dust, powders, dry particulates
- Non-vented safety goggles – mists, liquids
- Filtered lenses – infrared, UV, grinding, welding, lasers
- Face shields – secondary eye protection for flying debris, splashing; worn over primary safety eyewear to protect the face and divert from the eyes
- Research and sample PPE options with your safety distributor or manufacturer representative
- Eyewear should follow fit, feel, and function (shape/size, comfortable, protects from the known hazard)
- Include front-line employees in the sampling/selection process
- Do not limit selection to price; a better-quality selection may be less expensive if employees wear it
- Train employees on known hazards and the need for safety eyewear
- Impact on quality of life
- Impact of injury through recovery, pain, costs
- Implement accountability programs to reinforce positive outcomes
- Recognition for following procedures, working safely, encouraging others, finding and addressing hazards, when found
- Require employees, supervisors, and managers to properly perform their expected tasks through daily observations, performance reviews
- Find PPE that works – don’t chase “flavor of the month” eyewear
Employees will buy-in when you engage and guide employees in the selection process, like participating in sampling and giving feedback on choices. We can help support this through our TRACK program if you need help (it’s free!).
Much of the safety eyewear today meets the ANSI Z87+ standard but fails in end-user comfort, which results in a “cookie-cutter” template across numerous providers. Safety professionals may have multiple provider options, but the styles are very similar. This causes the selection process to focus more on price differentials with very little thought to the front-line employee wearing them.
Today, however, employers are no longer locked in to selecting “cookie-cutter” eyewear.
We have recently released Vision Safety Eyewear. What makes Vision unique? With the same care and reputation of our hand protection, the eyewear has been innovatively redesigned to properly fit the human form.
Taking more than two years in the design and development stages Vision eyewear is made from newly designed molds, using front-line employees in multiple industries to provide testing and feedback. Truly an innovative design, Vision meets the fit, feel, and function tests that encourages employees to wear the PPE that protects them from the identified hazards.
Summary
A safety eyewear program is only as effective as the employees who will wear it. Mechanix Wear® Vision Safety Eyewear offers employers an innovative way to get value and provide employees with effective protection, meaning it saves money by reducing injuries and claims, regulatory exposures and reduced employee exposures.
If you want help doing an assessment of your current eyewear and trial some new styles, click here.
If you know what you need and want to check out the options, click here.
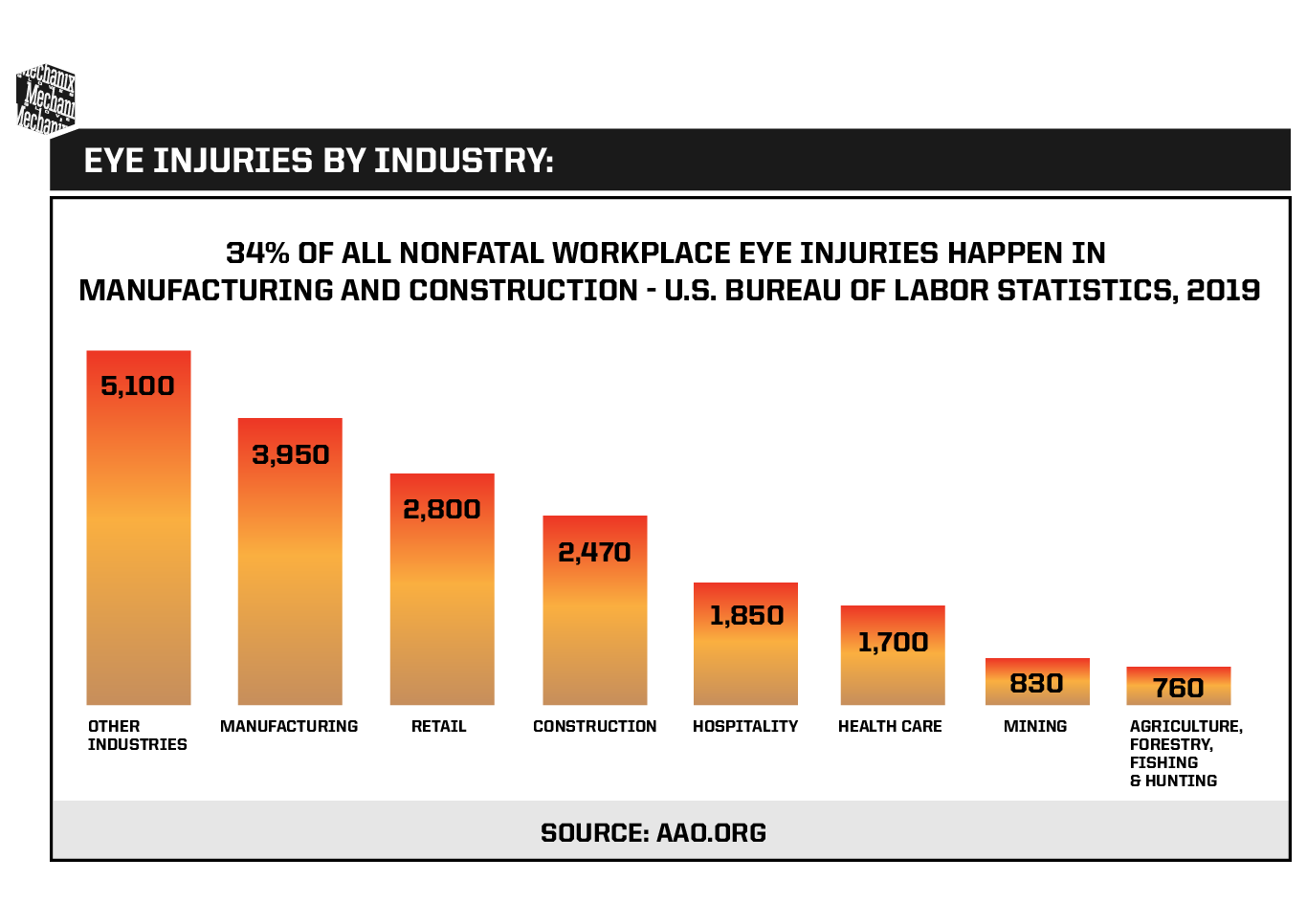