Building a Safety Culture or Safety Program: What’s the Difference?
The term “safety culture” is often used interchangeably with the term “safety program”. However, there are differences between the two.
A safety culture is a set of shared values and behaviors that guide an organization's response to safety concerns. It is an organization's culture with respect to safety.
A safety program, on the other hand, is a planned set of activities that are designed to help an organization create and maintain a safe environment for employees and others.
A company can have a great safety culture but not have any formalized programs in place. Conversely, they might have very good programs in place but not the culture needed to make them effective.
What is a Safety Culture and How Does it Help?
For an organization to be world-class in safety, there must be an effective and positive safety culture built into the values of the company. Safety cannot be a priority; it must be a value. This is not a matter of semantics. A ‘priority’ will change, depending on the circumstances. A ‘value’ remains constant, regardless of the circumstances. If you can identify a circumstance in which it is OK to remove safe actions to correct a problem, you do not have an effective or positive world-class safety culture.
When implementing a safety program, it must fit within your organization’s safety culture. The program does not make the culture; the culture determines the program. Behavior-based safety was all the flutter 25 years ago. Though the concept was great, the execution was a disaster for most companies. The reason? BBS was sold as a program that could be adopted without regard to the culture, the management style, or the level of employee engagement. It became cookie-cutter, following steps and actions that soon became the output, without regard to the culture or system.
It is ironic that many employers still advertise safety positions with the desire of having BBS experience, simply because they don’t recognize it as a failed program. The focus is on what they want the safety role to do rather than be there to create a positive impact on the organization’s culture and its people.
Developing, implementing, and maintaining a positive safety culture requires employee engagement and participation, supervisor and manager accountability, and a positive recognition program that encourages safe job performance. This is addressed through integrating safety into all your processes, procedures, and employee practices so safety becomes seamless within every level of the organization.

A safety culture produces actions out of a sense of value and contributes to the overall safety and well-being of every employee. A safety program produces actions based on what to “do.” If the program is not connected to the culture, that program is nothing more than a waste of time. If that program is based on punitive actions, there will be no buy-in, participation, or engagement at any level.
Every employer needs a safety program, but it must be designed and implemented through the value of safety. A safety “program” you buy off the shelf from a vendor will die before it ever works. It will become another flavor of the month that every employee knows won’t work because it is not built for that culture.
You can get ideas and suggestions from others’ programs that you can “adopt” and customize to fit your needs that keep safety fresh and interesting in your organization. Implementing an entire program, however, that was designed and met the needs of a different organization will be disastrous for yours.
How to Build a Predictive & Proactive Safety Culture
The next logical question is, how do I build an effective safety culture? The steps are simple, though the actual implementation is not always easy if you are already entrenched in a negative or punitive type system. In a nutshell, here’s what you need:
- KISS – Keep it Short and Simple. (Did you think we were going to say something different?). Complicated rules and actions are confusing and a waste of time. Simple steps may include implementing a real safety suggestion and recognition program, asking employees to conduct quick walkthroughs of their work area to identify and address hazards, and conducting inspections to observe employees doing things right.
- Compliance – Implement a hazard recognition and correction activity and you will comply with most regulatory requirements. Engage employees to help audit compliance documents so they better understand what the requirements are while learning the value of doing tasks right. Do NOT establish your culture on compliance alone; base it on hazard recognition and correction. That keeps the value on your people, not on an outside regulatory agency!
- Hazard Recognition – start with conducting a thorough PPE risk assessment. It’s an OSHA requirement and it is good business practice; the right PPE is selected and provided for the identified hazard(s). Ask front-line employees for help in identifying hazards and track them so the hazards are corrected, and actions taken are communicated back to the team.
- Contact Mechanix Wear via the TRACK program. Our professionals will be a second set of eyes for you and assist you in identifying hazards, providing solutions, and giving you samples of the right PPE for your front-line employees that match the identified hazards prior to purchasing anything. Allowing your people to participate will demonstrate to them your commitment to safety and your commitment to them. This creates positive goodwill and more participation.
- Actions – There are activities you can start today that can change or enhance your safety culture.
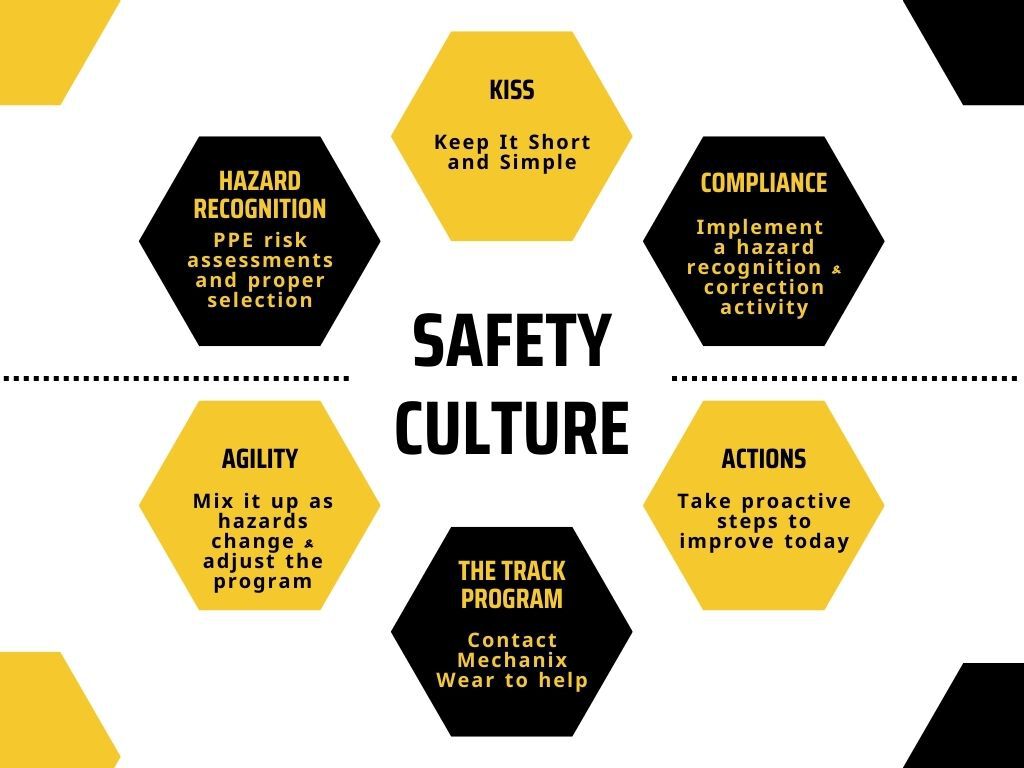
The 3 Essential Components of a Successful Safety Culture
- Workplace examinations: every person on your team should take 3-5 minutes prior to starting work to look for and address life-altering hazards. Ensure eyewash/shower stations, electrical disconnects, and fire extinguishers are clear and accessible; slips, trips, and fall hazards within designated walkways, stairs, and forklift aisles must be corrected. Let your team know the value of having them correct what they find prior to starting work so they are safer and better protected in the event of an emergency.
- Snapshot observations: take one minute during a shift to simply observe employee practices; recognize employees that are lifting correctly, using seatbelts, and wearing PPE while “encouraging” others to do the same.
- Conduct pre-task reviews: for an infrequent task, ensure all team members know their roles, understand their tasks, and have all the equipment and PPE needed prior to starting work. This review also works great for mentoring and training new employees.
A positive safety culture can be the difference between an organization with good intentions and one with real change. It’s not just about having a safety program in place but making sure that everyone in the company understands why it’s important to have one, and how they are a part of it.
Safety programs should change periodically to keep things fresh, based on your progress in becoming safer as your injury frequency and severity drop and your employees are fully engaged. Your safety culture should remain constant or improve as you focus on addressing hazards, providing positive recognition in employee performance, and encouraging employees to participate in safe practices. You can contact us today to sign up to the TRACK program and get ready for positive changes with your people and in your culture.